Operator / Facilities Manager | Reality capture for project communication
Description
Reality capture uses tools such as laser scanners and photogrammetry to create accurate representations of buildings and environments. These digital models serve as powerful communication tools, allowing facility managers to share precise, up-to-date information about the site with all stakeholders.
Improving project communication directly impacts health and safety during operations. Teams can virtually assess risks, plan maintenance, and coordinate activities more effectively, reducing on-site hazards. By providing a clear, shared understanding of the facility’s current state, reality capture supports better decision-making and promotes a safer work environment throughout the building lifecycle.
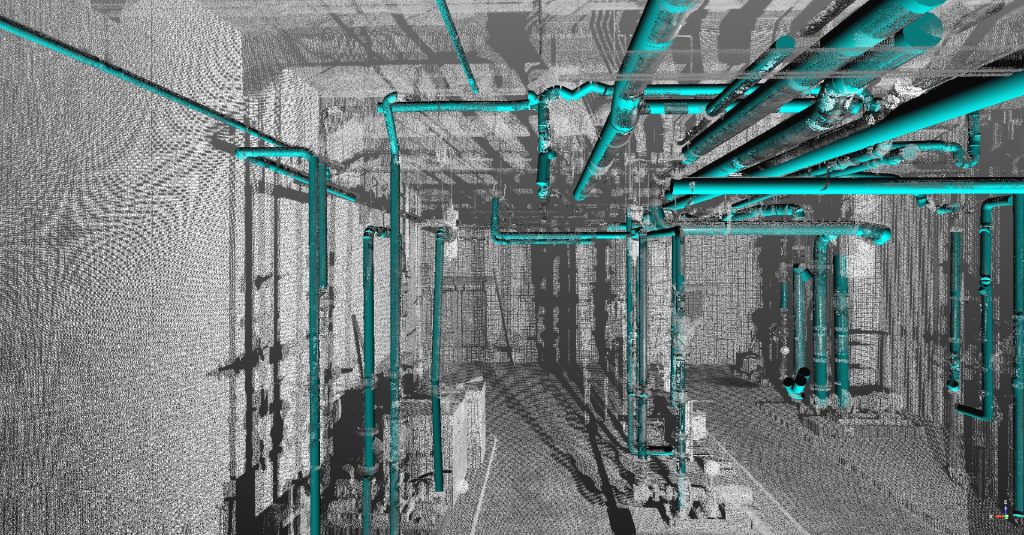
Model of a plant room based on a point cloud scan
By Oregon State University – https://www.flickr.com/photos/oregonstateuniversity/50513469887/, CC BY-SA 2.0, https://commons.wikimedia.org/w/index.php?curid=104962373
Case studies
Uses and benefits for health and safety
Examples of how reality capture can be used to enhance health and safety in facility operations through improved communication include:
- space
- Providing accurate 3D visualisations of hazardous areas, allowing safer planning of maintenance activities without physical exposure
- space
- Enabling virtual safety audits and inspections, reducing the need for personnel to enter dangerous spaces
- space
- Clearly communicating evacuation routes and emergency procedures through detailed facility models
- space
- Improving coordination between teams by offering a shared, accurate representation of the facility for discussing safety concerns
- space
- Allowing rapid identification and communication of structural changes or damage that may pose safety risks
- space
- Enhancing remote collaboration on safety issues, reducing the need for on-site presence in potentially hazardous environments.
Technology/techniques
Laser scanning, a key technique, uses lasers to measure distances and create detailed 3D point clouds, ensuring precise as-built documentation. Photogrammetry combines photographs to generate 3D models, offering a cost-effective alternative. BIM integrates reality capture data, fostering collaboration and communication among project stakeholders. Augmented Reality (AR) overlays digital information onto the real world, aiding in on-site decision-making. Mobile applications enable real-time access to captured data on handheld devices, enhancing communication efficiency.
Model/data requirements
Essential model data includes accurate geometric representations, spatial relationships, and asset details. Precise information about building components, equipment specifications, and maintenance schedules enhances communication between stakeholders and ensures that everyone is making decisions based on a common representation of the facility. Integration of as-built conditions, material properties, and real-time sensor data ensures a holistic understanding of the facility’s status.
Hardware and software requirements
Hardware components required include 3D laser scanners, drones, and cameras to capture spatial data. Advanced computers with substantial processing power are essential for data processing. Software tools like Autodesk Recap and Bentley ContextCapture enable data manipulation and model generation. Additionally, BIM software facilitates collaborative project communication. A reliable network infrastructure is necessary for seamless data transfer.
Contract/procurement implications
The contract implications involve incorporating specific provisions for reality capture services in construction contracts, addressing data ownership, liability, and the scope of capture. Procurement considerations include selecting vendors with expertise in reality capture and defining technical requirements. Effective project communication benefits from incorporating reality capture data into BIM, enhancing collaboration among stakeholders. Contracts should stipulate data-sharing protocols and standards to ensure seamless integration. Procuring reality capture services requires assessing vendor capabilities and aligning them with project needs. Overall, integrating reality capture into contracts and procurement strategies facilitates improved project communication, collaboration, and long-term facility management.
Roles and responsibilities
Facility manager | Oversees the implementation of reality capture technology, ensuring it aligns with safety goals and facilitates effective communication across teams.‎‎‎‎ |
Surveyor or reality capture specialist | Conducts 3D laser scanning or photogrammetry to create accurate digital representations of the facility, focusing on areas with potential safety concerns. ‎‎‎‎‎ |
BIM manager | Integrates reality capture data into the facility’s BIM model, ensuring up-to-date and accurate information for safety planning and communication. ‎‎‎‎‎‎‎ |
Health and safety officer | Uses reality capture data to identify potential hazards, plan safety improvements, and communicate risks effectively to all stakeholders. |
Maintenance team | Uses reality capture models for planning and executing maintenance tasks safely, providing feedback on any discrepancies between the model and actual conditions. |
Training requirements
Professionals in facility operation need training in reality capture technologies such as LiDAR, photogrammetry, and 3D modelling software. Understanding data acquisition, processing, and interpretation is crucial. Communication skills to convey project insights effectively are essential, ensuring seamless integration of reality capture for efficient facility management and operation.
Future directions
The future of reality capture for project communications in facility operation lies in advanced technologies like augmented reality (AR) and virtual reality (VR). Integrating real-time, immersive experiences with 3D models will enhance collaboration, streamline communication, and improve decision-making in facility projects.