Operator / Facilities Manager | Reality capture for inspection and monitoring
Description
Reality capture uses scanning technology to create a digital representation of real-world objects and environments. The digital model and the information it contains enables projects to more effectively manage operations and inspect and monitor facility operations.
Reality capture employs various techniques and tools, from manual observations to laser scanning, drones and photogrammetry. The captured information is usually incorporated into 3D models to provide accurate and detailed representations of the facility. Reality capture enables facility managers to assess structural integrity, track changes over time and identify potential health and safety issues in a virtual environment. The captured information can facilitate maintenance, and enhance safety, sustainable management and decision-making on facility operations.
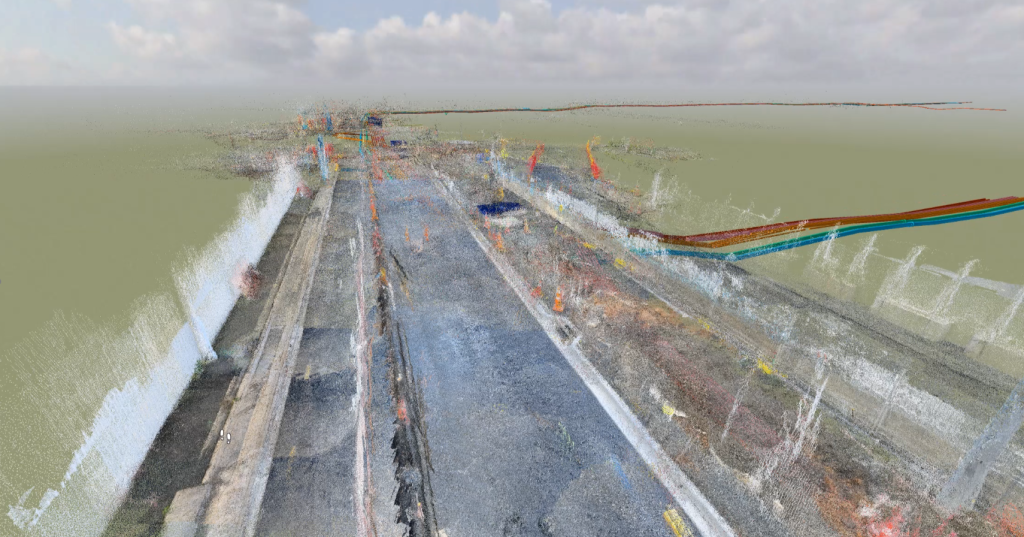
Point cloud capture of a facility, used to monitor current work against historical building records. Image provided by AIAL
Case studies
Uses and benefits for health and safety
Improves documentation of facility conditions, aiding in preventive maintenance and safety assessments.
Enhances decision-making and helps identify health and safety issues, such as structural damage or worn equipment.
Improves health and safety by enabling remote monitoring and reducing the need for personnel to be physically present on-site.
Other uses and benefits
Enhances collaboration among teams and assist design, retrofit and expansion projects by using accurate, as-built models.
Supports compliance tracking, cost estimation and asset management.
Optimises facility operations by streamlining maintenance and reducing operational costs.
Technology/techniques
Reality capture requires a form of scanning technology, such as a lidar or photogrammetry capture device. Lidar scanners use laser ranging techniques to record detailed, high-resolution point data. Photogrammetry combines many conventional still photographs to generate a 3D model of the environment.
The scanner may be carried by a person or mounted on a vehicle, such as an autonomous drone. Drone scanning is useful for capturing large sites and facilities.
Augmented and virtual reality help to visualise the captured data, enabling real-time analysis and remote monitoring. These tools enable facility managers to assess structural integrity, detect anomalies and optimise maintenance, improving safety and operational efficiency.
Model/data requirements
Data requirements for reality capture include accurate details about building components, materials and systems, as well as spatial relationships and asset information. Additionally, integrating real-time data from sensors and Internet of Things (IoT) devices can enhances facility monitoring.
Metadata, such as installation dates and maintenance history, provides a comprehensive understanding of assets.
Hardware and software requirements
The hardware required to carry out reality capture depends on the method and scale of the capture, but could include high-resolution cameras, lidar scanners, drones, and GPS devices to record detailed spatial data. Additionally, 3D laser scanners, sensors and thermal cameras can provide an even more comprehensive data collection.
To process and analyse this data effectively requires specialised software, such as Autodesk’s ReCap, RealityCapture or Bentley’s ContextCapture. These applications enable 3D modelling, point-cloud processing and data visualisation. Real-time monitoring requires IoT sensors and edge computing devices.
Together, this integrated hardware-software system provides accurate, up-to-date information for efficient facility operations.
Contract/procurement implications
Integrating reality capture tools into facility operations requires supporting equipment, software and expertise, which must be built into procurement budgets. Contracts must address data ownership, sharing and security concerns. As these technologies can streamline monitoring and enhance data accuracy, ongoing maintenance contracts may need adjusting.
Procurement teams should look for vendors with a good track record in reality capture.
Legal implications, including liability and intellectual property, need careful contractual consideration.
Roles and responsibilities
Facility manager | Oversees the integration of reality capture data into facility management processes, sets priorities for capture activities, and uses the data for decision-making. |
Surveyor or reality capture specialist | Conducts on-site scans, manages data collection, and ensures data accuracy. Operates scanning equipment and processes raw data into usable 3D models. |
BIM coordinator | Integrates reality capture data with existing BIM models, ensuring consistency and accuracy across digital representations of the facility. |
Health and safety officer | Uses reality capture data to identify potential hazards, plan safety improvements, and conduct virtual safety audits. |
Maintenance team | Uses reality capture models for planning and executing maintenance tasks, updating the models with as-built information after work completion. |
Training requirements
Operators must be trained to conduct advanced surveying techniques, laser scanning and photogrammetry, and to operate a drone. It’s essential that have experience with software like Autodesk’s ReCap and GIS mapping techniques.
Skills in data analysis, 3D modelling and facility management systems will enhance their proficiency in transforming captured data into actionable insights for efficient facility operations.
Continuous learning about emerging technologies in the field is also necessary to stay updated and proficient.
Future directions
Further advances in technologies such as lidar, autonomous drones and AI-driven analytics is expected to enhance real-time, accurate data collection for building monitoring, maintenance, and energy efficiency. Advances in augmented reality interfaces may also enhance user interactions, streamlining facility management processes for improved efficiency and sustainability.