Designer | Model interaction for project communication
Description
Model interaction during design helps project teams effectively communicate about safety. Instead of just looking at static drawings, teams can move through the virtual building, exploring spaces and spotting potential hazards. Layers can be switched on and off to explore issues that may only be visible for a particular subset of building elements. This hands-on approach makes it much easier for everyone – from designers to facility managers – to understand how the building will work in practice.
The ability to walk through and interact with the building model helps answer key questions about safe operation and maintenance. Teams can check access routes, measure clearances, and test whether equipment can be safely maintained. Making these checks during design, when changes are relatively cheap and easy to make, is far better than discovering problems during construction or after the building is complete.
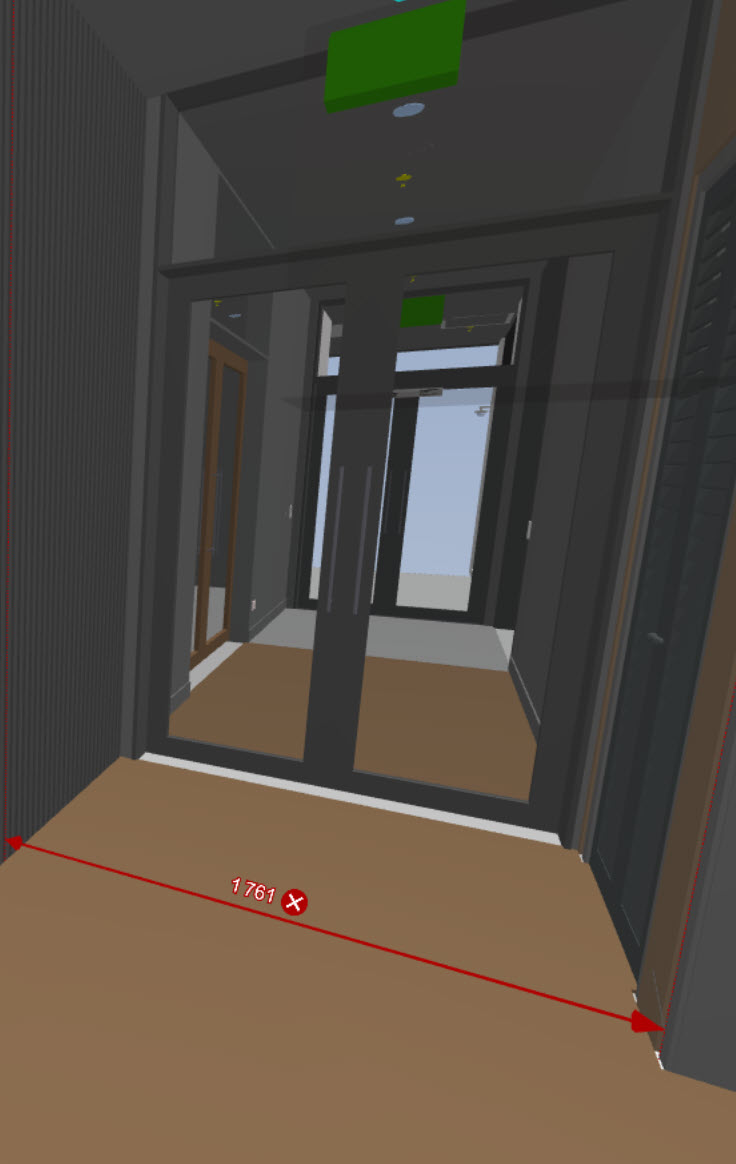
Using model interaction during design to check the width of a corridor
Case studies
Uses and benefits for health and safety
Using BIM models for communication during design brings several key advantages for safety:
- Design teams can work together more effectively by seeing exactly where building systems might clash and finding solutions before construction starts. This visual approach makes it much easier to spot potential safety issues.
- The model lets building users experience the space virtually before it’s built. For instance, school staff can walk through a digital version of their new building and point out any safety concerns about room layouts or lighting. This early feedback helps designers create safer, more user-friendly spaces.
- Facility managers can use the model to review plant and equipment placement during design. Their practical experience helps identify potential servicing or maintenance safety issues that might otherwise be missed. Early input from the operations team helps create buildings that are safer to maintain and operate throughout their life.
Technology/techniques
The BIM model created during design works alongside other visual tools like drone scans, point clouds, photogrammetry and online maps. Interactive tools let users do more than just look at the model – they can move through it, measure spaces, and highlight areas of concern.
Teams can mark up safety zones in the model to show areas needing special attention during inspections or monitoring. These might include access routes to emergency equipment or areas where maintenance work happens at height. Fire-rated structures can be colour-coded in the model and tagged with their rating details, making safety reviews clearer and more effective.
The model can also help create the project’s risk register. Safety hazards identified in the model can be tagged with relevant information, which then feeds directly into a digital risk register. This creates a clear link between the physical locations of hazards and their documentation.
Model/data requirements
Design teams need to create models at an agreed level of detail for their specific building elements. These individual models can then be combined to show the complete design. Most design phase modelling uses Level of Development (LOD) 100 or 200, which provides enough detail for effective communication about safety issues.
The most common file formats are Industry Foundation Class (IFC) and Autodesk’s Revit (RVT) format. If needed, conversion software can translate between different formats to ensure everyone can access the model. These standard formats make it easier to share models across the project team.
Hardware and software requirements
Model interactions can be created using a laptop or desktop computer. Visualisation software packages for interaction typically provide recommended hardware requirements for optimal performance.
Most viewing software provides options that allow stakeholders to interact with the model, for example to isolate specific elements, review associated data, and take measurements or projections within the model. Viewing software comes in two types – either locally installed on a computer or accessed via a web-based service. Mobile access on phone or tablet relies on web-based tools.
Many model viewing solutions offer online and offline access, which is useful for interacting with the model in the office, plant room or on site. It’s possible to interact with the model on several devices at the same time.
Contract/procurement implications
The design BIM Brief and BIM Execution Plan (BEP) detail how BIM will be used on the project. The BIM brief should clearly spell out how BIM will be used for safety communication. The BEP needs agreement from all design team members and should detail how models will be developed, what information they’ll contain, and how they’ll be used for safety reviews. Standard templates and processes are provided in the New Zealand BIM Handbook.
Costs for accessing and using the model must be agreed by all parties. Typically, the software and user allowances are defined in the BEP and contract. The contract can include how the visualisation will be accessed, when it will be updated and how many people can use it.
The New Zealand Construction Industry Council’s (NZCIC) guidelines can help structure BIM model requirements for each design stage. These guidelines provide a useful framework for including BIM requirements in contracts.
The contract should clarify that the BIM model is required for health and safety purposes and specify the exact uses, as well as who needs to be involved, for example, a requirement for a review of the model by the maintenance teams to be carried out during each design phase.
Roles and responsibilities
Design team |
Identifies safety hazards within the building. |
Design BIM manager |
Manages different design models, ensuring they are current and coordinate properly. ‎‎‎‎‎‎‎‎ㅤ |
Client/owner |
Responsible for eliminating, reducing and managing safety of the building. ‎‎‎‎‎‎‎‎ㅤ |
Project manager |
Manages and issues design milestone deliverables to the client, including safety in design (SiD) reviews and reports. ‎‎‎‎‎‎‎‎ㅤ |
Training requirements
Most project team members need minimal training to use BIM for safety communication. The client and non-BIM users might need basic training on viewing software, but this is usually straightforward. BIM modellers typically need no extra training as they’re already familiar with the tools. The Project Manager may need a short training session on interacting with the model but this usually takes less than half a day.
Future directions
Model interaction for safety communication continues to improve, especially as augmented and virtual reality become more common in design. These tools let project teams experience spaces virtually and provide more detailed feedback about safety concerns during design. This technology makes it easier for everyone involved to spot potential issues and contribute to creating safer buildings. Artificial intelligence algorithms and predictive analytics are being developed that assist in automatically identifying safety issues within design models or forecasting potential safety concerns based on design decisions, complementing human expertise.