Contractor / Subcontractor | Reality capture for hazard identification
Description
Reality capture is a technology that uses laser scanners, drones or photogrammetry to create a 3D digital representation of the surrounding environment.
Hazards are everywhere in a live construction site so is important for everyone on-site to know what the hazards are and where they are located. Reality capture can scan the whole site, and help the project team to identify and assess hazards prior to onboarding. Â This is an essential step, especially when working in remote locations, confined spaces, or on sites that lack precise rigging.
Combining reality capture and BIM models can help the project team look ahead to see what work is still to be done in an area, which can identify where current work may have introduced hazards for next stages of construction.
Case studies
Uses and benefits for health and safety
Provide a lookahead that compares the current state of the site with future work represented in the BIM model, to help identify hazards that may arise during the intermediate stages of the project.
Improve awareness of on-site hazards by communicating site information in a visual, more understandable format that accurately represents reality.
Better manage on-site hazards before work begins. The initial project team can capture the site and use it to better identify risks and plan for mitigation.
More accurately assess site conditions during works planning, enabling engineers to better identify the right equipment and resources for the job, and establish safer working methodologies.
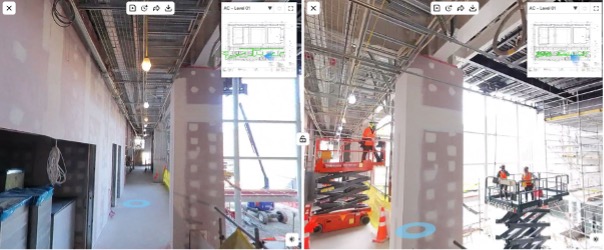
Reality capture using OpenSpace’s Capture software
Technology/techniques
Laser scanning is one method to reality capture an area. There are a few suppliers of laser scanning tools, including Leica and Faro. Both manufacturers offer an end-to-end approach, from devices for data capture through to software for view the resulting models.
Photogrammetry is another reality capture technology. It involves stitching together numerous still images to build up a spatial representation the whole site. The technology is widely used as a record-keeping tool, capturing day-to-day activities and progress on site.
Once the capture process is complete, the project team can view and annotate the 3D output, import it into authoring software, and use it in a variety of other ways to improve health and safety.
Model/data requirements
Reality capture itself does not require a BIM model, although software tools make it possible to combine the two technologies.
Reality capture is also a visual process, much like photography, and it requires suitable lighting on the subject to produce clear output with the most detailed graphics. It is also easily blocked by objects in its line of sight, such as people, vehicles and temporary structures. For the best results, capture at a time when these obstructions are at a minimum, such as during a lunch break when no one is working.
Hardware and software requirements
Many surveying companies offer laser scanners for hire. Trained operators invariably get better results, so companies often provide training for individuals to go along with the tool they hire.
Each scanner manufacturer provides its own proprietary post-processing software. It is possible to process reality capture data using widely used engineering software, such as Autodesk’s CAD tools, but it’s recommended to use the scanner manufacturer’s software for best results.
Contract/procurement implications
It’s common to use reality capture as a means to verify that the operational or as-built model agrees with all the actual build (this confirmation is known as achieving BIM Level of Development 500 or simply LOD 500). This requirement means the contractor must arrange laser scanning as part of their contract.
However, most contractors also use capture for other purposes, such as site assessment, record keeping, and to compare the design against on-site conditions.
Early in the process, all stakeholders must understand that using reality capture to identify risk is one of the objectives of rolling out digital engineering on a project.
Roles and responsibilities
Using reality capture to identify hazards involves several roles:
Surveyor |
Sets the targets and coordinate systems used link data from different sources. They can also stitch together data to represent part or all of the site. |
Site engineer or supervisor |
Conducts the on-site data capture. ‎‎‎‎‎‎‎‎ㅤ |
Health and safety personnel |
Uses captured data to identify hazards and mitigations, and communicates their findings to the trades and wider team. ‎‎‎‎‎‎‎‎ㅤ |
Training requirements
When using a laser scanning, training from either the manufacturer or supplier can give better results. It usually takes at least half a day to understand the basics of point cloud scanning and post processing.
Photogrammetry usually requires no more training than an on-boarding meeting, as it works just like a camera.
Future directions
Over the next few years, using reality capture to better identify and manage on-site hazards will become increasingly common. Demand for the technology is soaring due to the growing requirements for digital data and record keeping. Using reality capture to identify and manage risks during on-boarding will become part of a new starter checklist for any construction project.